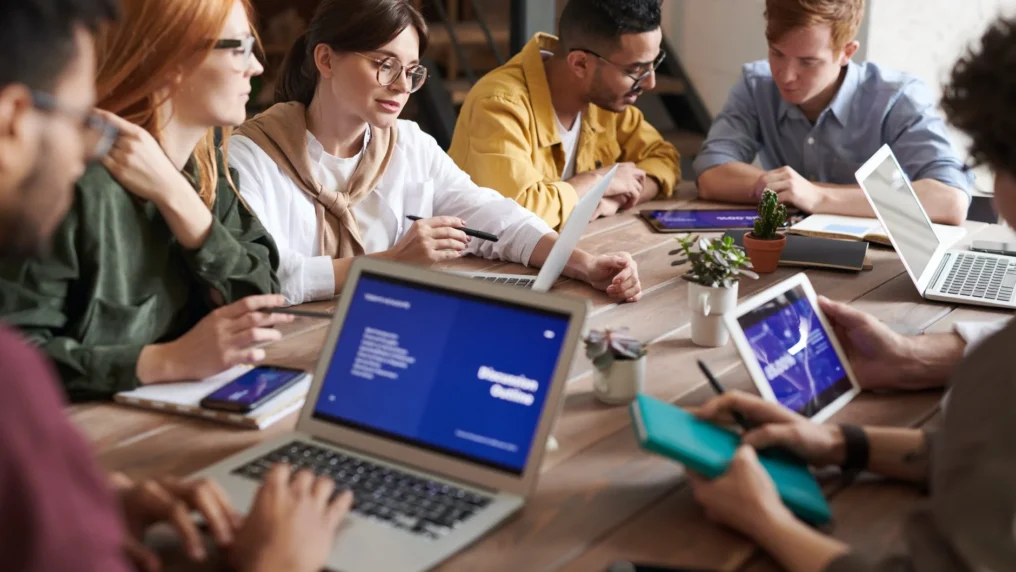
The past few years have seen business organizations optimize different aspects of their operations. The use of technology and software tools has enabled businesses to save time, cut down on redundancy, create affordable operational models and improve turnaround times!
Both large and small processes have been explored to their microcosm to understand where more success can be had. One such area where businesses have immensely benefitted is by using the right industrial scales for their organization.
It does not matter whether you are a big or small organization, a manufacturing entity, or a retail distribution unit, an industrial scale can benefit you equally. In this article, we are going to discuss the seven major benefits of investing and using industrial scales for your business.
What is an Industrial Scale?
The first thing that you need to know about industrial scales is that they are large units that are placed on the floor or on a ramp. This enables the easy loading and offloading of goods and products for the business. They are made of hard metals like iron, steel, and aluminum and are capable of withstanding heavy loads, often from hundreds of kilograms to a few metric tons.
An industrial scale can be hooked up to the computer and provide important data. This data in turn plays a crucial role in determining the inventory management processes of the business. If you are a business that is still using a regular scale to run your operations, it might end up costing you valuable time, effort, and costs!
Different business organizations ranging from manufacturing to distribution and warehousing can benefit by using industrial scales. For many businesses, this is what determines their costing and pricing strategies. This is a high-precision industrial tool that is dedicated to improving your business operations.
List of 7 Major Benefits of Using Industrial Scales for your Business Organization
1. Helps save on the wastage of raw materials-
There are several business organizations that require the precise measurement of raw materials to create finished goods. Using an industrial scale can help you with precision and accuracy. This will enable the optimum utilization of raw materials every time. Saving costs on raw materials can contribute to your bottom line and improve financial operations for the business.
2. Maintains the standard and quality of the final manufacturing batch-
Great businesses become successful as they are always able to maintain a high level of quality in their manufacturing process. The standardization of raw material quantity is what helps in stabilizing the quality of the final manufactured product. This ensures that every batch that is manufactured is the same as the last. Everyone from your customers to retailers will be happy.
3. Allows for the correct and accurate assessment of data-
Hooking up the industrial scale to the computer can unearth invaluable data for your business. This can help you process everything from raw material sourcing and purchase to stock taking, inventory management, and pricing. Using an industrial scale can also shed light on the losses to raw materials during production along with weighing the final goods after production.
4. Ultra-high precision enables better feedback and information-
No matter what kind of a business organization you are in, you are always looking to learn from and optimize your operations. An industrial scale can help give you feedback about strategies that can be implemented to improve your manufacturing, distribution, packaging, and sales. If you are working with a logistics partner like FedEx, you will be able to determine costs.
5. Sheds light on the cost of shipping the products or goods-
Every business worth its salt knows that shipping goods are not an inexpensive proposition. If you are looking to save costs on that front, you need to be aware of how much the shipping is going to cost you than being blindsided about the same and expecting to be shocked when UPS sends you the bill. An industrial scale helps you assess the costs of shipping beforehand.
6. Improve the workflow and operational efficiency in the business-
Workers that are responsible for weight raw materials and finished products will see their productivity improve. They do not have to worry about checking and double-checking all the time. They can simply use the precise and accurate nature of the industrial scale and move on. All the time saved will result in more work being done and add to the productivity of the business.
7. Sturdy and durable machines that last a lifetime-
If you are investing in premium-grade industrial scales, you can rest assured that they will last you for a long period of time. The best ones might be expensive but are less prone to breaking down or holding up your production process. Since they are made of solid metals, you do not have to worry about them getting damaged when a heavy load is placed on them.
The Final Word
If you are a business organization that is still in two minds about getting a new industrial scale for their business, this article might have helped you finalize your decision. An industrial scale can add tons of value to your operations. If you would like us to help you with any specific doubts or queries, please let us know in the comments below.
Read Also: