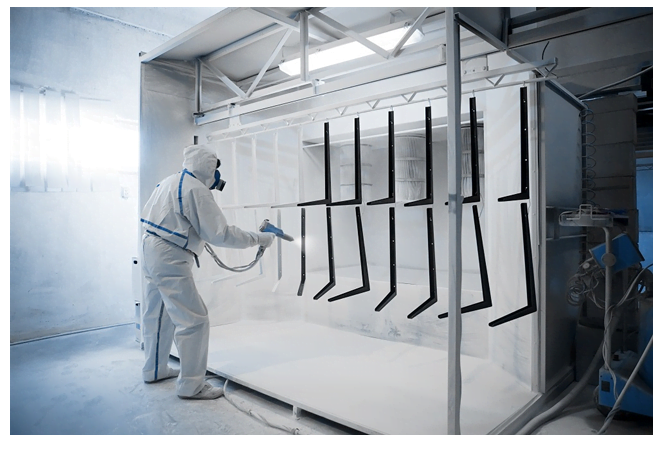
A thin complementary layer is applied to the exterior of a metal surface which is called Metal finishing. Various metal finishing themes are used particularly as per the different purposes of the business firm.
Application of The Metal Finishing Treatment Mainly Offers Specific Advantages to The Metal Products Such As:
- Enhanced durability
- Increased decorative appeal
- Improved electrical conductivity
- Better electrical resistance
- Greater chemical resistance
- More tarnish resistance
- Potential for vulcanization
Lots of manufacturing industries produce metal parts with different ways of Metal Finishing. Once the metal part has taken its final form of the product, metal finishing is applied to give a look of completion to it. As per the requirement and purpose of the product metal, finishing is executed which involves; altering the workpiece’s surface to attribute specific characteristic features. Paint, ceramic coating, Lacquer and other treatments are inclusive of one of the most common metal finishes.
Based Upon the Industry Trends’ Observation Below Mentioned Metal Finishing Kinds Are Found:
- Metal Plating
- Brushed Metal
- Buff Polishing
- Metal Grinding
- Metal Vibratory Finishing
- Sand Blasting
- Powder Coating
- Hot Blackening
The metal finishing procedures business area includes applying paints and coatings to metal surfaces. Companies are accumulating lots of benefits by running the process of applying paint through spray applications,electro-deposition, chemical baths, and other applications.
Two Kinds of Metal Finishing Industry Business Firms Are Found, Namely;
- Independent Metal Finishers– These are generally known as independent metal shops or job shops.
- Captive Metal Finishers– Consist of larger manufacturing units that carry out the rules of metal finishing processes.
Among the above two, Captive operations are found to be more accurate and specialized in their mode of operations. Their metal finishing processes are more efficient as they deal with a limited number of metal parts. The larger units limit their numbers of production and mainly concentrate upon fine-tuning their equipment for better operations for the coming days. Due to this, they have higher efficiency with very less amount of waste generated. Whereas the smaller Job Shops are less equipped and specialized in their respective operations as they tend to serve more customers, often with varied specifications and requirements. Although there is a considerable amount of difference between the two kinds of metal finishing business areas, they use the same technology hence the environmental impact also remains to be almost the same.
It may seem difficult to choose the right Metal Finishing Process for your project, anyhow there are few considerations that can help you to come up with the right kind of choices.
- Production Speed: It is essential to find out about the production speed, as time is very valuable and any delay or lag in production speed may hamper the whole project.
- Cost-effective: No matter how rich your company is or how much amount your company is ready to spend, if the process is not cost-effective then it’s of no use as such. Getting the right finishing machines may spend some bucks from your pocket but ultimately it may yield results at faster speeds.
- Metal Hardness: Metal hardness or softness has a greater impact on the choice of finishing techniques. As the harder metals need intense finishing techniques, such as grinding, or tough abrasives in comparison to softer materials.
On a whole, metal finishing processes are dealt with by different industries in their respective ways. These techniques may vary based upon the requirements in relation to what kind of business do you have or what kind of project do you deal with. Instead of following the trends or being tempted by alluring finishing designs; it is much preferable to have the choice based upon the business need of your own.
Read Also: